北京时间2022年3月22日晚23点,特斯拉德国柏林超级工厂举行开工仪式。作为特斯拉在欧洲的第一座工厂,柏林工厂除了加快特斯拉在欧洲的订单交付步伐,更重要地,马斯克奉行的“第一性原理”将再次在生产端得以实践--前后一体压铸式车身工艺、4680电池和CTC电池车身一体化技术。
其中,被外界视为技术变革又一风口的CTC电池车身一体化技术也在柏林产Model Y和比亚迪海豹、零跑C01的渐次曝光中,得到更大范围的关注。
在搞明白CTC技术之前,我们先来了解一下什么是CTP技术,以及他们之间的联系。
CTP技术全称为Cell To Pack,通过取消模组设计,直接将电芯集成为电池包,电池包又作为整车结构件的一部分集成到车身地板上。
这种方式减少了模组本身的侧板、端板(模组结构件)和原本用于分隔模组以及帮助模组连接的横梁、纵梁(电池包装配支撑结构)等材料,整个电池结构极大简化,利用空间得到释放,同等尺寸的电池包容量得以扩展、电池组质量得以减轻,由此带来电池能量密度的提高和成本的降低。
CTP技术现有两种不同的路线。一是彻底取消模组的方案,以比亚迪刀片电池为代表;二是小模组整合为大模组的方案,以宁德时代CTP技术为代表。
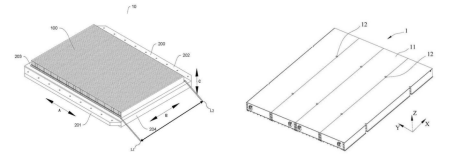
比亚迪刀片电池 vs 宁德时代CTP(图片来源:企业专利)
2019年9月,宁德时代全球首款CTP电池包量产下线,搭载于北汽EU5车型。较传统电池包,其CTP电池包体积利用率提高了15%-20%,电池包零部件数量减少40%,生产效率提升了50%,能量密度可达到200Wh/kg以上。
比亚迪紧随其后,于2020年3月发布其创新技术刀片电池。简单而言,将电芯宽度无限拉长,厚度做薄,实现900mm甚至快1m的超长电芯,与传统方形电池相比,呈现“扁平”和“长条”形状。
两大头部动力电池大力推动下,CTP技术经过2020年的小规模试水,到2021年,已在多款爆款新能源乘用车上成熟应用,实现规模生产。在此背景下,2022年,将开启CTP电池规模应用元年。
一方面,2021年以来,宁德时代CTP电池包相继在特斯拉Model 3、Model Y、小鹏P7、蔚来ES6等高性价比爆款车型规模导入。此前公开宣布搭载CTP电池的蔚来ET7也将于本月底开启交付。
另一方面,比亚迪亦明确宣布旗下全系车型搭载刀片电池。2021年比亚迪乘用车销售近60万辆,2022年计划推出不少于20款新车,包括汉DM-i、秦Plus DM-i、宋MAX DM-i等爆款车型的DMi版本。
与此同时,蜂巢能源推出的短刀电池,同样也将会以CTP的形式实现配套,目前已经确定搭载在欧拉车型上。
除方形CTP电池外,包括捷威动力远景动力等软包电池企业也在积极探索CTP方案。其中,捷威动力基于软包大模组概念推出的积木电池技术已成熟,送样国际车企,国内规模推广在即;远景动力软包CTP同等空间内电池容量将增加一倍,续航延长至1000km,预计2024年量产。
CTC技术全称为Cell to Chassis,宁德时代董事长曾毓群之前在中国汽车蓝皮书论坛上是这样介绍它的:“此技术将电芯和底盘集成一起,再把电机、电控、整车高压如DC/DC、OBC等通过创新的架构集成在一起,并通过智能化动力域控制器优化动力分配和降低能耗。CTC将使新能源汽车成本可以直接和燃油车竞争,乘坐空间更大,底盘通过性变好。”
CTC在某种意义上可理解为CTP的进一步延伸,其核心在于省去模组、打包过程,将电芯直接集成到汽车底盘上,实现更高程度集成化。
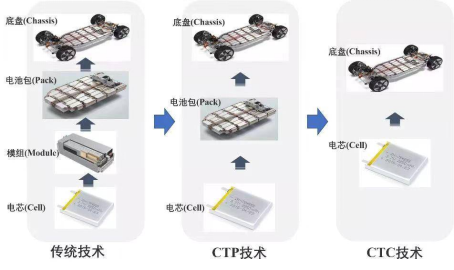
传统技术 vs CTP vs CTC(图片来源:电动势)
但是,CTC又非CTP的简单延伸。CTP并没有突破PACK本身,电池企业/专业PACK企业可以独立完成开发,技术并没有延伸至下游。而CTC的出现,将突破PACK的限制,直接涉及到汽车底盘,这是整车最为关键的核心部件,是整车厂商经历长期发展所积累的核心优势所在,是电池企业/专业PACK企业难以独立开发的。
纵观国内外所有潜在玩家,目前最接近量产的依旧是“先驱者”特斯拉。
特斯拉去年在柏林工厂举办的Giga Fest活动中,展示了4680 Structural Battery(CTC)方案--4680电池包取消了模组设计,电芯密集排布在车辆底盘中,电池上盖肩负密封电池与车身地板两项功能,座椅则可直接装在电池包上。
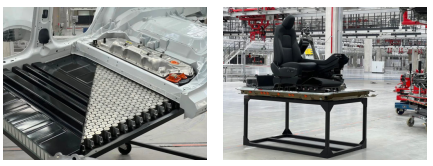
宁德时代正在加快CTC的研发攻关,并宣布计划于2025年左右推出自己的CTC方案,并有望于2028年升级为下一代智能化CTC。
比亚迪只是在非官方口径中,不经意透露海豹将搭载CTC技术。而此前e平台3.0发布的重要时刻,也仅仅是将这一点用“电池车身一体化”一笔带过。
就目前来看,零跑汽车有望成为国内厂商中最先吃到螃蟹的厂商。2022年2月25日,零跑汽车正式发布了一款全新汽车--零跑C01的预告图。动力系统方面,零跑C01将成为首款搭载CTC电池技术的量产车型,将于2022年第二季度正式发布。

目前电动汽车最重要的技术指标,也是消费者关注度高的,是汽车的续航里程,而对续航里程最直接的影响就是电池电量,因此增加电池电量就成为增加汽车续航里程的最有效方案。为了实现更高的电量,电池的集成趋势已经由小模组发展为大模组、超长模组,甚至无模组方案,这种方式已经在一定程度上提升了空间利用率,增加了电量。但是为了追求更苛刻的需求,所以提出结构化电池的概念,让电池本身成为车身的一部分(类似现代民航飞机将整个机翼作为油箱的思路),也就是CTC,也称为电池车身一体化。
CTC技术是目前纯电动车电池与整车集成的发展趋势,然而要推广CTC并非易事。特斯拉CTC技术的公开展示为行业内CTC发展指引了方向,或将迫使电池厂商加快CTC研发和落地进度。目前,宁德时代正在大力招聘汽车底盘技术相关的人才,这可能与其CTC布局有关;国轩高科也与车企讨论过CTC方案,认为这在有限的范围内可行,但目前还没有布局;蜂巢能源表示,从技术上来看CTC完全可以实现,但目前重心仍然在CTP上。电池企业缺乏对车辆底盘的开发经验和技术积累,虽然在CTC上有构想,但若想在底盘技术上有所突破还需要较长时间的积累。
原文始发于微信公众号(锂电产业通):动力电池包技术:从CTP到CTC
新能源汽车的快速发展带动了动力电池的高速增长。动力电池生产流程一般可以分为前段、中段和后段三个部分。其中,前段工序包括配料、搅拌、涂布、辊压、分切等,中段工序包括卷绕/叠片、封装、烘干、注液、封口、清洗等,后段主要为化成、分容、PACK等。材料方面主要有正负极材料,隔膜,电解液,集流体,电池包相关的结构胶,缓存,阻燃,隔热,外壳结构材料等材料。
为了更好促进行业人士交流,艾邦搭建有锂电池产业链上下游交流平台,覆盖全产业链,从主机厂,到电池包厂商,正负极材料,隔膜,铝塑膜等企业以及各个工艺过程中的设备厂商,欢迎申请加入。
长按识别二维码关注公众号,点击下方菜单栏左侧“微信群”,申请加入群聊