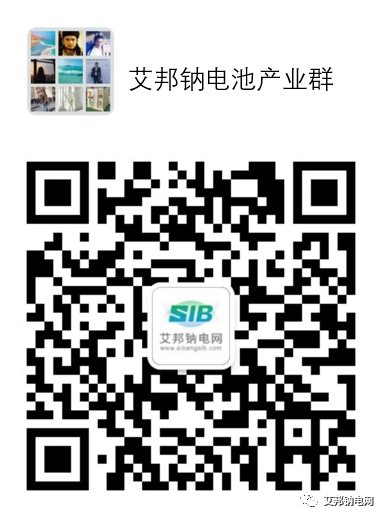
性能优势:石墨掺硅能带来比容量的显著提升
负极的比容量反应的是储锂电能力,石墨负极上限为372mAh/kg,而硅定理论比容量达到4200mAh/g,但由于硅负极存在的膨胀性问 题,目前产业内最佳的策略是制备硅碳混合掺杂负极材料,因而硅碳负极的比容量提升是循序渐进的。掺杂的硅负极有硅碳、硅氧两种路线,硅碳即单质硅为基体再与碳材料复合,硅的添加比例在1-5%左右,优点在于容量及首充效率高, 但循环性能较差;硅氧将纯硅和二氧化硅合成一氧化硅制备负极材料,牺牲了一定容量提升循环性能,但首充效率低。
技术路径:硅氧相对易产业化,硅碳负极逐步推进
硅氧负极因循环及比容量优势率先产业化应用:硅氧负极主要指氧化亚硅SiOx材料,储锂过程中生成纳米Si、Li2O及锂硅酸盐,生成的 Li2O及锂硅酸盐主要抑制纳米Si颗粒发生团聚,起到缓冲体积膨胀的作用,故而循环性能优异,同时生成的Si也提高了材料的比容量,但 由于Li2O的不可逆锂损失也使得硅氧材料的首效较低,目前杉杉,贝特瑞,特斯拉等率先使用的也是硅氧材料。硅碳负极突破循环限制后将加速追赶:硅碳材料具有首效及比容量高的优势,但是膨胀性问题使得其循环寿命500-600圈,无法达到 1000圈的动力电池要求,未来随着包覆技术的改进,循环性能改善后硅碳材料将加速追赶。
技术路径:传统球磨法,新工艺看PVD、CVD产业化
硅碳负极材料制备工艺复杂,由于材料膨胀性问题,需要将硅粉做到球状、 高纯度、粒径小、分散度高的纳米级,制备方法包括球磨法、CVD(化学 气相沉积法)以及PVD法(物理气相沉积法)。目前主流的方法为球磨法, CVD与PVD处于送样阶段。
发展现状:硅碳渗透率1%-2%,仍处于起步阶段
负极分技术路线来看,人造石墨仍然为主流负极产品,2020-2021年渗透率达到82%-85%;其次是天然石墨,占比约14%;硅碳负极方面,根据GGII数据,2021年硅碳负极出货约1.1万吨,相比于负极74万吨出货量,目前渗透率仍只有1.5%,横向来看2018- 2021年硅碳负极出货量CAGR达61.7%,但渗透率仍处于1-2%区间内。(报告来源:未来智库)
瓶颈因素Ⅰ:膨胀性是产业化进程缓慢的重要原因
膨胀性问题是硅碳负极大范围应用的最大阻碍,同时膨胀性带来的巨大体积变化,一方面使得电极内部应力积累,造成电极粉化,降低 电池的循环性能以及安全性,另一方面体积变化也使得负极的SEI膜需要反复形成,损失活性锂源,降低首次库伦效率。目前产业内主要通过纳米化、碳包覆、金属掺杂等方式来改善硅碳负极的膨胀性问题,同时硅氧负极也能够在一定程度上改善硅的膨胀 性,但是离达到产业化标准还有一段距离。
瓶颈因素Ⅱ:首次容量损失,补锂弥补缺陷
硅碳负极的第二个瓶颈是首次效率较低,首充效率低主要是硅的膨胀性导致 的,一方面可以通过纳米化等方式降低硅碳负极的膨胀性,进而减少活性锂 损失,提高首充效率;另一方面可以通过正极或者负极补锂的技术,来补偿 损失的活性锂,提升硅碳负极首充效率。
瓶颈因素Ⅲ:硅碳有溢价,但单耗摊薄降低成本
硅碳负极有溢价,能量密度提升有望摊薄度电成本:硅基负极纯品价 格差异较大,少则15-20万元,多则数十万元;考虑混品后的售价相比 人造石墨负极仍存在单吨6-8万元溢价,但是硅碳负极带来的能量密度 的提升能在在电池材料的用量上带来摊薄效应,未来考虑硅碳负极均 价下降后,硅碳负极电池的度电成本有望实现性价比。
产业化进度:圆柱先行,方形加速追赶
在硅基方案的产业化应用上,特斯拉+松下是最早实现大规模量产的,得益于圆柱路线的优势;不过方形硅基方案的配套上车,也在稳 步推进,预计在2022年前后有望实现;而在车企中长期规划中,硅基方案会作为重要的考量。(报告来源:未来智库)
产业化进度:贝特瑞领先,优质负极企业积极跟进
负极厂:主流负极厂如贝特瑞, 杉杉股份,璞泰来,中科星城 等均有硅碳负极技术储备,产 能方面贝特瑞目前拥有硅基负 极产能3000吨/年,杉杉璞泰 来进展较快,均实现年千吨级 别出货,其他材料厂也纷纷布 局硅碳负极产能,
02 快充:产业趋势明朗的升级
技术原理:负极锂离子嵌入速率影响倍率性能
充电过程为活性锂离子从通过电解液电子通过外电路正极向负极转移,快充即是加快锂离子的转移速度,一般通过加大电流密度的方式 实现,但当加大电流带来的锂离子的转移速度高于负极锂离子内嵌速度时,便会在负极表面出现锂堆积的情况,进而造成电池短路,所 以负极与电解质界面处以及负极颗粒中的固相扩散速度对快充性能影响较大。
技术原理:实现快充核心解决容量保持、散热问题
容量保持率低&高温:加大电流后锂离子嵌入速度加快,当锂离子嵌入速度大于材料传递速度时,锂离子便会在负极表面形成锂金属, 一方面会造成嵌入石墨中的锂离子减少,造成电池容量保持率低,另一方面锂枝晶存在刺破隔膜的可能,造成严重安全问题,同时电流 加大后也会造成温度上升过快。材料创新&热管理:材料体系创新包括石墨负极的性能改进以及硅碳负极、电解液等电池体系的改进,主要是为了改善电池容量保持率 降低的问题,同时由于温度过高,对于电池的热管理系统也需要创新。
材料革新Ⅰ:包覆碳化&元素掺杂实现快充性能提升
石墨材料为二维层状结构,锂离子必须从材料的端面嵌入,导致扩散 路径较长,改善石墨负极快充性能的方案包括:1)孔隙结构:通过如 强碱在石墨表面刻蚀产生纳米孔隙增加扩散路径,但难度较大,容易 破坏晶体结构;2)表面包覆(即碳化):软硬碳的层间距离比石墨稍 大,通过在石墨表层包覆一层无定形碳或者其它碳材料改善石墨倍率 性能;3)元素掺杂:通过加入B、S等改善石墨的电子状态,使其更 容易得电子,进一步增加锂离子的嵌入量。
材料革新Ⅱ:天然人造混合方案亦可提高快充性能
宁德时代采用“天然+人造“方案实现3C快充:从专利内容上看,宁德时代将天然石墨设置在负极集流体上,将人造石墨覆盖在天然石 墨上达到快充效果,天然负极:人造负极质量比在0.7-0.9之间,倍率性能上看电池支持3C快充,容量保持率在90%以上。杉杉天然人造混合方案支持2C以上快充:杉杉将人造天然石墨混合后石墨化碳化处理得到复合石墨负极,人造石墨:天然石墨质量比在 5:5-7:3之间,复合材料兼顾低膨胀及2C以上快充性能。
材料革新Ⅲ:硅碳高理论容量带来优异的倍率性能
xC是个相对概念,与材料比容量相关,石墨比容量以360mAh/g来算,对应0.1C的电流密度就是36mA/g,10C电流达到360mA/g,随 着电流密度的提升,部分锂没办法及时嵌入,所以造成可逆容量下降,理论比容量的上限限制了石墨负极在更高倍率下充电。硅碳负极倍率性能理论上要好于石墨。硅碳负极理论比容量在4200mAh/g,在20A/g的电流密度下实际比容量在812 mAh/g,对应倍 率性能为25C,超高的理论比容量使得硅碳负极的倍率性能优于石墨负极。(报告来源:未来智库)
热管理:麒麟、4680无极耳推出,加速快充落地
宁德时代2022年发布麒麟电池,其中最大的变化是水冷板设计从底部调整为电芯最大面积侧的冷却,进而使得换热面积增加了4倍;特 斯拉4680电池的无极耳工艺提高了电芯散热能力,蛇形管冷却+顶部水冷的方案,也有助于快充的导入。从电池厂4C快充的产业化进程看,宁德时代宣布采用麒麟电池方案在2023年上市,欣旺达、孚能科技也有积极的规划。
产业化进度:车企聚焦800V方案,加速快充迭代
国内外车企纷纷推出支持快充技术的车型,不同企业间快充技术的方案各有差异,如广汽推出石墨烯超级技术,规划推出6C—500km、 3C—500km两个版本的快充电池,2021年9月首次搭载在广汽埃安AIONV上,而保时捷采用硅负极方案提高快充性能。
03 软硬碳:钠离子引发的变化
软硬碳:钠离子电池负极理想材料
锂离子电池负极材料不适用于钠离子电池:由于Na+半径较大,传统的石墨材料无法满足高储钠能力,石墨作为钠离子电池负极材料时, 由于钠-石墨化合物热力学不稳定,形成的钠碳化合物仅提供31mAh/g的容量。软硬碳:无定型碳根据是否能被石墨化分为软硬碳,软碳(可石墨化)拥有短程有序的石墨化微晶结构利于插层储钠,优势在于价格低, 安全性能好,但由于高电压平台使得电池能量密度低,同时存在可逆钠容量不足短板;硬碳(不可石墨化)得益于较大的层间距离和晶 格缺陷,拥有更多可逆储钠点位,表现出较高的可逆容量、稳定的结构以及长的循环寿命,但倍率性能及首次效率较差,目前对硬碳的 储钠机制仍有争议,主流厂商多使用硬碳材料作为钠电池负极材料。
软硬碳:制备工艺上不再需要石墨化过程
无定形碳通常由有机前驱体在500-1500℃温度下热解产生,无需石墨化过程,热解后的最终产物是硬碳还是软碳,主要取决于前驱体 的性质。热固性前驱体(富氧或是缺氢),例如聚偏二氯乙烯、木材、纤维素、羊毛、酚醛树脂、棉花、糖类或环氧树脂等,在热解过 程中发生固相碳化,容易形成硬碳。热塑性前驱体(富氢或者缺氧),例如聚氯乙烯、聚苯胺、石油化工原料及其下游产品(煤碳、沥 青和石油焦等),在热解过程中发生熔融碳化,有机高分子发生重排,容易形成软碳。
来源:沥青基碳材料
新能源汽车的快速发展带动了动力电池的高速增长。动力电池生产流程一般可以分为前段、中段和后段三个部分。其中,前段工序包括配料、搅拌、涂布、辊压、分切等,中段工序包括卷绕/叠片、封装、烘干、注液、封口、清洗等,后段主要为化成、分容、PACK等。材料方面主要有正负极材料,隔膜,电解液,集流体,电池包相关的结构胶,缓存,阻燃,隔热,外壳结构材料等材料。 为了更好促进行业人士交流,艾邦搭建有锂电池产业链上下游交流平台,覆盖全产业链,从主机厂,到电池包厂商,正负极材料,隔膜,铝塑膜等企业以及各个工艺过程中的设备厂商,欢迎申请加入。
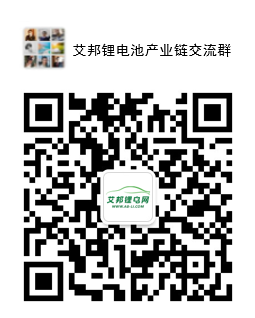
长按识别二维码关注公众号,点击下方菜单栏左侧“微信群”,申请加入群聊