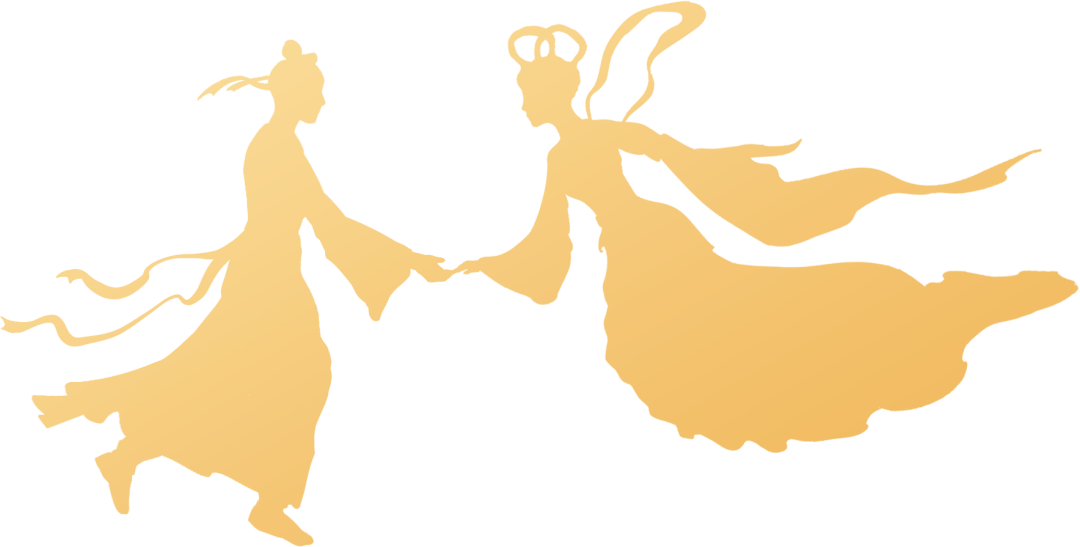
1、PET基膜为当前复合
铜箔主流技术路线
PET、PP、PI三者在在热性能、化学性能、机械性能、电性能具有不同的特点,导致其 复合铜箔产品特点各有差异:
1)PET长期使用温度在-70℃-120℃之间,短期使用可达 150℃,其韧性在所有热塑性材料中最优,但PET化学性能较差,不耐酸碱,因此易溶于 电解液;
2)PP最突出的性能在于其化学稳定性,几乎不与酸碱反应,抗腐蚀性能优越, 因此常用于制作各种化工管道与配件,除此之外,由于PP的密度小于PET,理论上减薄空 间大于PET,PP材料的劣势在于热性能较差并且与铜的界面结合力小于PET;
3)PI各项性 能较为突出,目前多用于特工材料。PI薄膜具有高强度、高韧性、耐高温、防腐蚀等特 殊性能,在-270℃-300℃温度之间仍能保持出色的强度、刚度、隔热和电气绝缘性,由 于其成本较高,PI目前主要应用于航空、航海、宇宙飞船、火箭导弹、原子能、电子电 器工业等领域中。
基膜材料的性能不仅影响产品特点,对复合铜箔制作的工艺需求及所需设备也有要求。PET与PP已实现产品出货,两种材料在制备铜箔时的主要差异表现为抗拉强度、耐热性以及与铜的界面结合力上。
1)抗拉强度影响涂附工序:PET抗拉强度大于PP,PET拉伸比 为3.3~3.5,而PP拉伸比9.0~10.0,在进行涂附工作是PET工艺更简单;
2)耐热性影响工 艺温度:蒸镀是通过高温融化金属,使其蒸发到基膜上实现镀铜,耐热性低的基膜材料 在蒸镀工艺中容易被烫损或卷皱,PET为饱和线形大分子,分子主链上没有支链,结构对 称,满足紧密堆砌的要求,因此易于取向和结晶,导致PET具有高熔点、高强度,操作难 度要小于PP;
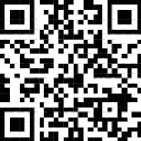
两步法为当下主流
由于高分子基材与铜膜结合力较差,叠加极薄基材易击穿、烫损等原因,复合铜箔镀铜 工艺难度较大。由于高分子材料与金属材料之间缺少化学键和,基材与金属铜之间的结 合力较差,若铜膜在电池循环过程中脱落,将严重影响电池的循环性能及安全性能,此 外,对于复合铜箔来说,镀膜的工艺会影响产品的均匀性、柔韧度、延展性和抗氧化性。镀铜工艺通常选择磁控溅射、蒸镀或水电镀,对基材的柔韧性、耐热性要求较高。因此, 如何在不损伤基材的情况下提高铜膜的附着能力成为制备复合铜箔的主要难点。
目前市场常用的镀铜工艺主要有“两步法”与“三步法”两类流程。其中“两步法”工 序流程为磁控溅射+水电镀,首先,通过磁控溅射(PVD),在塑料薄膜表面镀上一层金 属层(大约15-40nm),使其能够导电并保证膜层具有较好的致密度和结合力;其次,再 通过水电镀的方式,将金属层加厚至1μm;“三步法”以“两步法”为基础,在水电镀工序前增加蒸镀,利用蒸镀加速金属层的沉积。
“一步法”显露头角,分为一步式全湿法与一步式全干法。一步法有望通过减少工艺 步骤,从而提高产品生产良率与镀膜均匀性。一步全湿法指仅利用化学沉积的方式沉积 铜膜,一步全干法指仅利用磁控溅射或真空蒸镀方式镀铜。
目前两步法以良率较高、成本压力低等综合优势,产业化进程较快,有望在消费电池上 优先进行应用。“三步法”在两步法的基础上增加蒸镀流程加速高分子材料“金属化”, 因此在生产效率上优于“两步法”,但同时新的流程及设备的引入将会增加工艺成本, 除此之外由于不同设备涂覆的铜膜具有均匀度、紧密度等方面差异,对产品良率也有影 响。“一步法”的设备工艺尚未成熟,且成本较高,目前量产难度较大。
(1)真空设备镀膜
磁控溅射原理
磁控溅射具有沉积速率可控、结合力强等优点,但在效率、镀膜均匀性、良率等方面仍 存在较大的提升空间。磁控溅射可以通过控制溅射电压、电流和功率灵活控制沉积速率, 其高速溅射的原子或分子也能够更稳定的附着在基材表面,结合力较强。但同时磁控溅射的沉积效率较低,单次溅射的镀层只能达几纳米,40纳米铜膜需要重复二十几次;并且在磁控溅射中,由于难以保证氩离子均匀轰击靶材,从而不能保证镀膜的均匀性;最后,磁控溅射对靶材的消耗量大,利用率低,且磁控溅射过程需要高压放电,可能存在膜穿孔现象,从而影响产品良率。真空蒸镀同样是一种物理气相沉积(PVD)方法,通过在真空环境下加热铜金属,使大量的原子或分子蒸发并沉积在基膜表面。真空蒸镀是在真空环境下使用蒸镀设备加热铜 金属,使其以原子团或分子团的形式蒸发并沉降在高分子基膜表面。
(2)水电镀增厚镀膜
(3)化学镀膜
化学镀铜在良率、纯度、镀膜均匀性等方面表现较好,但结合力较差、沉积速率过慢且 成本较高。根据三孚新科公告,复合铜箔化学沉积工艺将由新工艺、新设备、新材料(专 用化学品)三个核心要素组成,具有较优的良率、纯度、以及镀膜厚度均匀性,工艺简 单、维护成本低等优点,其劣势在于结合力较差、沉积速度过慢,并且湿化学品用量、 废水排放量相对较大,环境维护成本较高。
(报告出品方/作者:川财证券,孙灿)
原文始发于微信公众号(锂电产业通):复合铜箔行业处于产业化初期,工艺路线百花齐放
新能源汽车的快速发展带动了动力电池的高速增长。动力电池生产流程一般可以分为前段、中段和后段三个部分。其中,前段工序包括配料、搅拌、涂布、辊压、分切等,中段工序包括卷绕/叠片、封装、烘干、注液、封口、清洗等,后段主要为化成、分容、PACK等。材料方面主要有正负极材料,隔膜,电解液,集流体,电池包相关的结构胶,缓存,阻燃,隔热,外壳结构材料等材料。 为了更好促进行业人士交流,艾邦搭建有锂电池产业链上下游交流平台,覆盖全产业链,从主机厂,到电池包厂商,正负极材料,隔膜,铝塑膜等企业以及各个工艺过程中的设备厂商,欢迎申请加入。
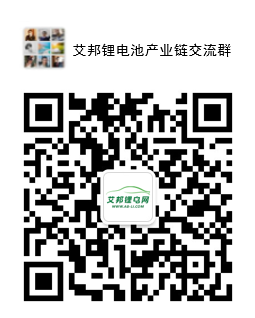
长按识别二维码关注公众号,点击下方菜单栏左侧“微信群”,申请加入群聊