电池包壳体轻量化,对于提升电池包能量密度有着重大意义。
研究以铝合金型材为主体结构的电池包壳体,对铝合金型材断面、搅拌摩擦焊接接头、连接工艺等方面进行了分析研究,并在成本、工艺性等方面进行综合比较,通过CAE对设计方案进行分析验证。
合理的结构设计和连接方式,可以有效地保证壳体整体强度,降低加工难度,使壳体减重,为电池包壳体的轻量化设计提供参考。
经过近几年的高速发展,目前我国已成为世界新能源汽车产销第一大国。随着国家2019年新能源汽车补贴政策的出台和续航里程要求的提高,对电池系统能量密度提出了更高的要求。
提升电池能量密度有两种路径:一是增加单体电芯的比能量;二是电池包的结构轻量化。提升单体电芯的比能量,技术难度大,研发周期长,资金投入大,相比之下,使电池包的结构轻量化则更容易实现。
铝合金在汽车上的应用早已屡见不鲜。铝合金具有密度低、比强度高、热稳定性、耐腐蚀性及导热性良好、无磁性、成型容易、回收价值高等诸多优点,因此是电池包轻量化设计的理想材料。
目前,电池包壳体用材主流方案是挤压铝合金壳体+PP/玻纤复合材料上盖。
就目前发展来看,铝合金壳体和塑料上盖的方案具有轻量化前景。壳体采用铝挤压型材 + 搅拌摩擦焊 + MIG焊的方案,综合应用成本低,性能满足要求,且可实现水冷电池的循环水道的集成。
上盖采用非金属上盖,主要用到PP/玻纤 + LFT-D模压工艺,既能提高生产的效率也可满足火焰燃烧和密封性能的要求,且模具成本较低。
铝合金电池包壳体已在多款新能源汽车上应用,例如,比亚迪宋和唐、蔚来 ES8、北汽EV系列等。该壳体可提升电池包能量密度,增加续航里程。由此可见,铝合金电池包壳体具有广阔的市场前景。
典型的铝合金拼焊电池包壳体如图1所示。壳体主要由铝合金型材边框和铝合金型材底板构成,采用6系挤压型材拼焊而成。
为保证焊接强度和密封性,选用低应力变形小的搅拌摩擦焊,铝合金型材适用的标准件一般有钢丝螺套、拉铆螺母、压铆螺母。
除标准件外,其余为100%铝合金材质。该壳体强度高、重量轻、耐腐蚀性好。
边框和底板为铝合金挤压型材,材料一般选用6061-T6(屈服强度 240 MPa, 抗拉强度260MPa)、6005A-T6(屈服强度215 MPa,抗拉强度255 MPa)和6063-T6(屈服强度170 MPa,抗拉强度215 MPa)等,根据断面复杂程度、成本、模具消耗等因素考虑具体选用何种牌号。
这几种材料的强度大小,依次为:6061-T6>6005A-T6>6063-T6,同等断面挤压难度为:6061-T6>6005A-T6>6063-T6。
图 2 是边框的典型断面,由多个空腔组成,材质为6061-T6,壁厚最薄处 2 mm。
边框主要有两种加工方案:一是进行整体型材挤压,然后机加工,零件一体性好,强度有保证,但加工量大,成本较高;另一种是采用型材拼焊的方式,此种方案成本较低,但焊缝强度较弱,需要验证焊缝强度是否满足要求。
图 2 边框断面
图 3 是底板的典型断面,由多个空腔组成,包括上部凸起,上部凸起主要用于电池模组的安装。
因断面尺寸较大,且厚度只有2mm,所以选择材质6005A-T6。上部凸起如需要安装钢丝螺套,可将上部空腔做成实心。
非安装部位可用CNC设备去除,在保证强度的同时,能使重量最轻。
边框和底板是电池模组的承载者,对强度要求比较高,所以一般都选用具有型腔的双层断面来保证强度,底板厚度一般为10mm左右,壁厚2mm。较少使用单层铝板。
6063-T6由于材质偏软,主要用于复杂断面或者受力较小的零件。
铝合金电池包壳体的主要连接方式有:搅拌摩擦焊接、MIG、拉铆、压铆以及少量弧焊和胶粘。
底板与底板、底板与边框主要用搅拌摩擦焊连接。焊缝强度可达母材80%左右。
搅拌摩擦焊接与普通熔焊方案相比较,具有以下突出的优点:
-
-
焊接接头质量好,焊缝为细晶锻造组织结构,没有气孔、裂纹、夹渣等缺陷;
-
-
焊接效率高,在 0.4-100 mm 厚度范围内可以实现单焊道焊接成型;
-
-
-
焊接成本低,没有焊接过程消耗,不需要填丝和保护气体;
-
图 4 为底板型材搅拌摩擦焊接接头,底板与底板之间采用板对接接头双面焊接。双面焊接强度高,变形小。
在搅拌摩擦焊接过程中会对工件有一个很大的下压力,所以,就需要增加型腔内筋和圆角厚度,焊接深度越大,筋和圆角就越大。
边框和底板之间主要有两种连接方式:一是双面搅拌摩擦焊接;二是外部搅拌摩擦焊接和内部弧焊 + 涂胶。
图 5 是边框与底板双面搅拌摩擦焊接接头形式。为给搅拌头预留出足够的空间,边框与底板连接处伸出长度要足够长,避免边框和搅拌头干涉,以免增加边框型材的尺寸和挤压难度。但双面焊接强度高、变形小,这也是它的主要优势。
图 6 为外侧搅拌摩擦焊接+内侧MIG焊接。底板外侧需搭接在型材边框上,且型材边框搭接处应做成实心,满足搅拌摩擦焊接要求,给焊接提供支撑力;内侧则采用MIG焊接,视情况选择满焊或者断续焊接。
此种连接方式效率高、难度小、成本低,但是因为内部采用了弧焊,焊缝可能有漏水的风险,所以,还要再涂一遍密封胶来保证密封性,这也是它的一个弊端。
图 6 边框与底板外部搅拌摩擦焊接+内部MIG焊接
由于整车行驶环境的复杂性,尤其是电池包安装在车辆底盘下方或者位置较低的区域,当电动车辆遇到涉水、暴雨等危险工况时,可能会因水汽的侵袭导致电池的电气故障、短路、漏电等危害,因此必须为电池系统提供防水、防尘的环境。
电池包的密封性直接影响到电池系统的工作安全,从而影响到电动车辆的使用安全。
通常,电池包密封防护等级要求达到IP67才能保证电池包密封防水,这样电池组才不会因为进水而短路。
铝合金电池包壳体的底板与底板之间宜采用搅拌摩擦焊接。由于搅拌摩擦焊接属于固相连接技术,在焊接过程中金属基材不融化,因此,相比熔化焊接减少了气孔、裂纹等缺陷的发生率。所以,为了较好地保证密封性,焊接应优先选用此种焊接方式。
如果边框与底板内部采用弧焊,则需要涂焊缝密封胶来保证密封性。壳体与上盖之间虽然采用发泡硅胶来保证密封,但是,连接的标准件自身也要保证其密封性,壳体法兰一般采用M5拉铆螺母。
目前,已有厂家生产可以专门用于电池包的防水密封的表面带胶的拉铆螺母,通过拉铆螺母塑性变形,使胶起到密封作用。
前端使用的盲孔压铆螺母,由于自身具有一定的密封效果,且外部附件也有密封圈,所以不再做单独处理。
表2为某款钢质电池包壳体铝化的情况。从表2数据可知,减重效果达到26.7%。电池包壳体的铝代钢不仅可以提升电池包能量密度,也增加了车辆续航里程。
根据GB/T 31467.3—2015电动汽车用锂离子动力蓄电池包和系统第三部分:安全性要求与测试方法,对铝合金电池包壳体强度、振动、挤压等方面进行仿真分析。
-
图 7(a)3G 向前工况应力最大值为 29.4 MPa,
-
图 7(b)振动应力最大值为55.98MPa,最大值均小于6005A屈服强度215 MPa,
-
图 7(c)挤压最大位移7.081 mm,电池模组安全距离为10mm(每个电池包结构不同,安全距离也会不同,需要客户确认),满足要求。
1、6061-T6 和 6005A 两种材质的性能均可以较好地满足设计要求。
2、挤压断面结构的一体化虽然加工量大且成本高,但有利于电池包强度的提高,可综合考虑。
3、搅拌摩擦焊接在保证焊缝强度的同时还可以保证密封性,是电池包壳体的最佳焊接方式。
5、型材拼焊的铝合金电池包壳体具有成本低、减重效果好等特点,减重效果在25%以上,可应用于新能源汽车上,提高电池包能量密度,延长续航里程。
锂电产业通公众号里的内容包括锂电池产业链交流、资讯、人脉圈。从正负极材料生产到涂布,隔膜、电解液、封装材料到检测组装等这些环节涉及的材料、辅材、添加剂、耗材,以及相关设备,相关企业介绍。想了解锂电更多相关信息,欢迎各位关注本公众号,后续可第一时间获取相关资讯!
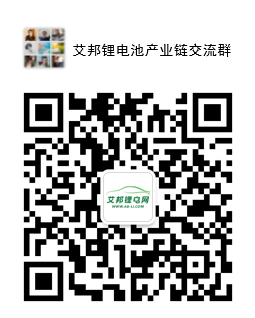
长按识别二维码关注公众号,点击公众号下方菜单栏左侧“微信群”,申请加入群聊
活动推荐1
【邀请函】全国动力锂电池产业高峰论坛(12月16日 深圳)
序号 |
议题 |
演讲企业 嘉宾 |
1 |
绿色低碳转型背景下电池材料供需与产业链安全 |
刘刚 教授 |
2 |
锂电池热失控安全报警技术 |
同济大学 王磊 教授 |
3 |
锂电材料分析检测以及真空解决方案 |
安捷伦 |
4 |
AI深度学习在锂电检测领域的应用 |
东莞兆丰 罗桂勤 副总经理 |
5 |
三元锂电池的研究与应用 |
拟邀:宁德时代,欣旺达,蜂巢能源等 |
6 |
磷酸铁锂电池的研究与应用 |
拟邀:比亚迪,国轩高科,亿纬锂能等 |
7 |
软包电池发展趋势及研究现状 |
拟邀:孚能科技,LG新能源等 |
8 |
圆柱电池升级之路 |
拟邀:松下,特斯拉等 |
9 |
电池结构创新技术分析 |
拟邀:中创新航,广汽,零跑汽车等 |
10 |
电池包外壳创新设计 |
拟邀:和胜股份,旭升股份,格瑞德等 |
11 |
动力电池管理系统BMS及其安全功能解析 |
拟邀:格瑞普,力高技术,华霆动力等 |
12 |
固态电池发展趋势及研究现状 |
拟邀:北京卫蓝,重庆太蓝等 |
13 |
固态电池产业链分析 |
拟邀:星盈科技,金龙羽,台湾辉能等 |
14 |
锂电池设备升级核心竞争力 |
拟邀:先导智能,赢合科技等 |
15 |
锂电全工序生产流程及关键设备 |
拟邀:金银河,施耐德等 |
16 |
锂电全工序关键检测设备 |
拟邀:凌云光,星云股份等 |
17 |
激光切割技术升级 |
拟邀:海目星,大族激光等 |
18 |
废旧锂电池回收利用现状及思考 |
拟邀:格林美,邦普循环等 |
19 |
退役动力电池梯次利用技术与市场拓展 |
拟邀:中伟股份、骆驼股份等 |
20 |
动力电池回收拆解装备需求 |
拟邀:天奇自动化等 |
如果您有创新主题演讲意向,请与我们联系!
联系人:吕子涵
电话:13048836648(同微信)
报名方式
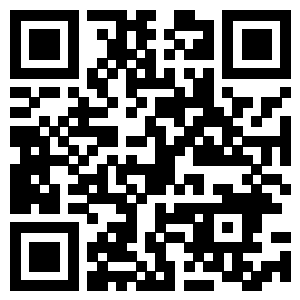
活动推荐2
【邀请函】第二届新能源汽车电池高分子材料高峰论坛(12月15日 深圳)
序号
|
拟议题
|
嘉宾单位
|
1
|
锂电池负极粘接剂的性能要求与发展趋势
|
弗迪电池
|
2
|
锂电池隔膜的最新市场情况及星源材质产品开发
|
星源材质
|
3
|
锂电池隔膜先进涂覆工艺和设备的重要作用 |
卓高电子(璞泰来) |
4
|
干法隔膜在长寿命磷酸铁锂电池中的应用
|
中兴
新材
|
5
|
纤维素基隔膜材料在动力电池领域的应用 |
中科院煤化所
|
6
|
PVDF基聚合物电解质制备及其性能研究
|
中科院
重庆研究院
|
7
|
高性能锂电池负极水性粘结剂的性能研究
|
绿能纤材(重庆)
|
8
|
电池模组的进化及改性塑料的应用
|
上海普利特
|
9
|
高性能铝塑膜开发及软包电池未来趋势
|
邀请中
|
10
|
气凝胶在电池包热管理中的应用
|
邀请中
|
11
|
缓冲/隔热/阻燃/密封泡棉在动力锂电池中的应用
|
邀请中
|
12
|
电池包壳体材料SMC生产工艺及其发展趋势
|
邀请中
|
13
|
胶粘剂在动力电池中的应用
|
邀请中
|
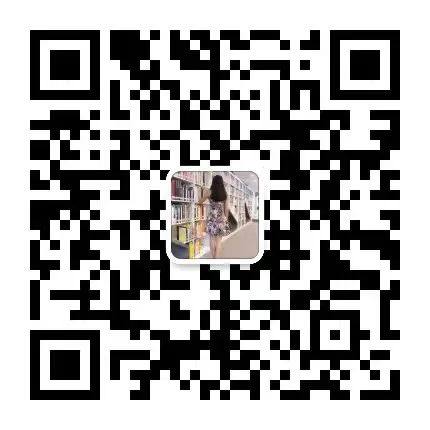
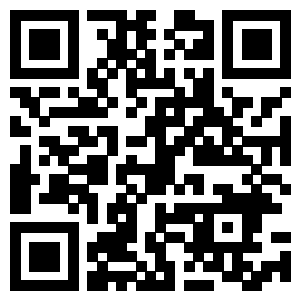
原文始发于微信公众号(锂电产业通):电池包解析:壳体结构设计及连接工艺
新能源汽车的快速发展带动了动力电池的高速增长。动力电池生产流程一般可以分为前段、中段和后段三个部分。其中,前段工序包括配料、搅拌、涂布、辊压、分切等,中段工序包括卷绕/叠片、封装、烘干、注液、封口、清洗等,后段主要为化成、分容、PACK等。材料方面主要有正负极材料,隔膜,电解液,集流体,电池包相关的结构胶,缓存,阻燃,隔热,外壳结构材料等材料。
为了更好促进行业人士交流,艾邦搭建有锂电池产业链上下游交流平台,覆盖全产业链,从主机厂,到电池包厂商,正负极材料,隔膜,铝塑膜等企业以及各个工艺过程中的设备厂商,欢迎申请加入。
长按识别二维码关注公众号,点击下方菜单栏左侧“微信群”,申请加入群聊