01
锂电集流体向轻薄化、低成本、高安全性趋势发展
减薄趋势下,锂电池存在安全隐患,复合集流体材料有望打破瓶颈。越薄的锂电集流体 其抗张能力和抗压变形能力越低,箔面出现断裂或裂缝的可能性较大,从而容易引发热 失控。同时,传统集流体在受外力碰撞时容易产生毛刺,进而引发短路等安全隐患,因 此兼具安全性等优势的复合集流体有望成为未来的发展趋势。
传统集流体是由纯度较高的单金属或合金制成,目前在锂离子电池集流体材料的选择上, 使用较多的为铝箔和铜箔,其作用是承载电池正负极活性物质,并将活性物质产生的电子汇集起来形成电流对外输出;而复合集流体是一种以高分子基膜材料作为中间层,两 边分别以其他功能金属作为镀层的一种夹层状导电薄膜材料,当前使用较多的为复合铜 箔及复合铝箔。
相较于传统集流体,复合集流体在材料构成、工艺原理以及性能特点等方面均有不同:
1)材料的构成上,传统集流体通常以高纯度的单金属或合金制成,比如传统铝箔由电 解铝制成,电解铝含铝量在 99.5%-99.8%之间,而复合集流体原材料包括高分子材料 (PET/PP/PI)、金属材料与粘结剂;
2)工艺原理上,传统铝箔使用辊压方式,经过粗轧、 中轧、精轧等流程最终轧制成片材;传统铜箔主要包括延压法和电解法,前者利用塑性 加工原理通过对高精度铜带反复轧制-退火而成,后者通过硫酸铜溶液在直流电的作用 下,利用电解设备电沉积而成;而复合集流体以蒸镀、水电镀工艺为核心,利用蒸镀、 水电镀技术将金属材料涂覆到基材表面。
02
复合铜箔:适用于对能量密度要求较高的电池产品
复合铜箔是指以高分子材料为中间层,两边分别以金属铜为镀层的薄膜材料。目前复合铜箔中间层的主要路线包括 PET、PP、PI 三种,不同的高分子材料由于具有不同的各项 性能,因此其下游应用场景也具有差异。
PET、PP、PI 用作复合铜箔的基膜材料时各有优劣:PET 综合性能最好,但不耐酸碱易 溶于电解液;PP 密度低,集流体减重上限更高,对电池能量密度提升明显;PI 性能最 优,但成本较高。
具体来说,PET 材料具有较强的韧性和较好的热性能及电绝缘性,常用于制作热收缩膜、抗静电膜、高光亮膜、反光膜、化学涂布膜等材料;PP 材料的突出 优势在于其化学性能稳定,通常用于制作各种化工管道及其配件;PI 材料性能突出,具 有极强的耐热性、电绝缘性和优良的机械性能,但成本较高,主要应用于航空、航海、 宇宙飞船、火箭导弹、原子能、电子电器工业等各个领域。
复合铜箔在安全性能、原材料成本以及对电池能量密度提升方面优势明显,契合锂电池集流体发展方向。复合铜箔使用高分子材料置换传统铜箔中的部分金属铜,高分子材料 相对于铜材,能够有效的增强集流体的韧性与绝缘性,减少金属铜的使用量,进而减小集流体的厚度与重量,为正负极活性材料提供更多空间。
1)高安全性:抑制锂枝晶生长,穿刺时阻断电流防止热失控
电池系统热安全事故主要表现为电池热失控,电滥用、机械滥用和热滥用均能引发电池 热失控。电滥用是指锂电池过充电、过放电容易引起锂枝晶生长,枝晶穿刺隔膜将会导 致正负极相接,进而引发电池短路;机械滥用是指电池在外力作用下发生形变,如碰撞、 挤压、穿刺、振动等,容易导致隔膜被破坏,电池正负极短路而诱发热失控;热滥用是 指锂电池在高温环境下长时间工作,会使得隔膜在高温下瓦解,进而导致电池短路。
复合铜箔能有效抑制锂枝晶生长,穿刺时阻断电流防止热失控。复合铜箔使用高分子材 料作为中间层,在动力电池处于电滥用或机械滥用环境中时,一方面,柔性高分子材料 的应力松弛机制能够使得锂均匀沉积从而抑制锂枝晶生长,避免薄膜断裂产生毛刺,另 一方面,即便电池发生短路,材料的电绝缘性能够降低电池短路电流,改善电池的安全 性;此外,当动力电池处于高温环境或发生热失控时,由于高分子材料在热源影响下, 会向远离热源方向收缩,进而牵引靠近热源的铜膜远离热源,自动切断失效电路。
2)低成本:铜材使用量减少,高分子聚合物成本更低
复合铜箔能缩减金属铜用量,进而减少箔材单位面积成本。传统铜箔在“铜价+加工费” 模式定价下,原材料成本占比较大。根据中一科技 22H1 报告披露,原材料占标准铜箔 及锂电铜箔各类产品单位成本比重基本处于 70%-85%区间。根据我们测算,以 6.5μm 的 复合铜箔为例,每平米原材料成本为 1.26 元,相比于 6μm 传统铜箔原材料成本下降 65%,相比于 4.5μm 传统铜箔成本下降 54%。
3)高能量密度:复合铜箔能够减小集流体重量,从而提升电池能量密度
复合铜箔使用低密度的高分子材料置换部分金属铜,能够降低集流体重量和厚度,从而 提升电池能量密度。复合铜箔在保证导电层导电性能和集流性能前提下,一方面,可以 利用高分子材料的韧性等特点减薄集流体厚度,即不影响电池安全性能又能够扩大正负 极活性材料的体积;另一方面能够降低集流体重量,从而提高电池能量密度。根据比亚 迪的实验数据,负极采用 3μm 的基膜+上下各 1μm 铜箔层的复合集流体,电池能量密 度较 6μm 的传统铜箔集流体可提升 3.3%;若正极也采用复合集流体,电池能量密度可 合计提升 6.1%。
03
复合铜箔成本测算:规模化量产后,复合铜箔成本优势显著
上游铜价高位上行,推动铜箔降本进程加速。近年来上游铜价持续上涨,自2020年初至 今,铜价涨幅达到40%左右,原料端降本需求日益增强。价格方面,2022年长江有色金属 网铜均价为6.75万元/吨,同时PET材料平均价格为0.84万元/吨。相比之下,PET材料价 格仅为铜价的1/8左右,且复合铜箔用铜量小,对金属铜依赖降低,理论上PET复合铜箔 单位材料的用铜量仅为传统铜箔的1/3左右。随着PET复合铜箔工艺逐步成熟和良率持续 提升,后期形成规模效应后其降本空间较为明确。
相比于传统铜箔,PET复合铜箔的原材料成本可下降64%,单位面积重量可下降68%。由 于PET等基膜成本较低,经测算,6.5微米(4.5微米PET+2微米铜)复合铜箔的原材料成 本为1.3元/m 2,较6微米传统铜箔低64.23%;单位面积重量较传统铜箔下降67.67%。其中, 测算的假设为:1)铜价采取2022年长江有色金属网铜均价,约为6.75万元/吨;PET基膜 价格为0.84万元/吨;2)假设铜靶材价格为铜价两倍,铜靶材溅射的铜厚度为60纳米, 靶材利用率为100%;3)铜和PET的密度分别为8.96g/cm³和1.38g/cm³。
传统铜箔成本主要由原材料成本和加工费组成,其中原材料成本占比最大。在传统铜箔 企业“铜价+加工费”的定价模式下,铜原材料成本占生产成本中的绝对多数。以传统铜 箔制造企业铜冠铜箔、嘉元科技为例,2021年铜箔生产成本中原材料成本占比约为83.7%, 人工成本占比约为2.8%,制造费用占比约为12.5%,运杂费占比约为0.9%。
传统铜箔单位面积综合成本约为 3.91 元/平。根据铜冠铜箔和嘉元科技 2021 年年报数 据,传统铜箔平均生产成本为 7.3 万元/吨,以铜密度 8.96g/cm³计算,则传统铜箔单位 面积综合成本为 3.91 元/平。假设原材料成本、加工费(人工成本+制造费用+运杂费) 分别占比为 84%、16%,则单位面积原材料成本为 3.3 元/平,单位面积加工费为 0.6 元 /平。
复合铜箔的成本主要由原材料成本、设备折旧成本和加工费组成。在复合铜箔制造过程 中,原材料价格、设备的生产效率、产线的良率以及产能利用率等因素都会对复合铜箔 的生产成本产生较为明显的影响。同时,工艺路线的选择对复合铜箔生产成本的影响也 较大。其中,两步法由磁控溅射和水电镀工艺组成,其生产工艺相对一步法更为成熟, 成本更低,但设备效率和良率仍有较大提升空间;而一步法是纯化学的工艺,其镀膜的 均匀性和良率较高,但目前生产工艺尚未成熟,生产速率慢且成本较高。随着后期设备 线速度、良率、产能利用率的提升,预期未来复合铜箔综合成本有望降至3元/平以内, 成本优势得以显现。
两步法关键假设:
1) 情景一:实现小规模生产(产能利用率为70%),良率达到80%的情况。1、工作时间:工作天数为300天/年,工作时间为16小时/天,年小时数为4800小时。2、磁控溅射设备:假设设备价格为1500万元/台,宽幅为1.3米,线速为13米/分钟。3、水电镀设备:假设设备价格为1000万元/台,宽幅为1.2米,线速为8米/分钟。4、人工和其他费用:以铜冠铜箔、嘉元科技2021年成本占比的均值为例,人工和其 他费用比例约为16%。考虑到复合铜箔技术为新型技术,其人工及制造费用较高,因 此假设其他费用比例为19%。
2) 情景二:实现规模化量产(产能利用率为80%),良率达到85%的情况。1、工作时间:工作天数为330天/年,工作时间为24小时/天,年小时数为7920小时。2、磁控溅射设备:假设设备价格为1200万元/台,宽幅为1.3米,线速为15米/分钟。3、水电镀设备:假设设备价格为800万元/台,宽幅为1.2米,线速为10米/分钟。3) 情景三:实现规模化量产(产能利用率为90%),良率达到90%的情况。1、磁控溅射设备:假设设备价格为1000万元/台,宽幅为1.3米,线速为20米/分钟。3、水电镀设备:假设设备价格为600万元/台,宽幅为1.2米,线速为12米/分钟。
经测算,在情景一和情景二的情况下,两步法复合铜箔综合成本分别为3.7元/平、2.6元 /平。随着复合铜箔设备和工艺的持续优化迭代,在情景三的理想情况下,两步法复合 铜箔综合成本可以降到2.26元/平,相较于3.91元/平的传统铜箔,整体成本可下降42% 左右。
一步法关键假设:
1) 情景一:实现小规模生产(产能利用率为50%),良率达到90%的情况。1、工作时间:工作天数为300天/年,工作时间为16小时/天,年小时数为4800小时。2、药水:假设药水成本为3元/平。3、设备:由于公司设备暂未定价,假设化学镀铜设备价格与水电镀设备价格一致, 为1000元/台,宽幅为1.5米,线速为2米/分钟。4、人工和其他费用:以光华科技、三孚新科2021年成本占比的均值为例,人工和其 他费用比例约为9%,因此假设其他费用比例为12%。
2) 情景二:实现规模化量产(产能利用率为60%),良率达到95%的情况。1、工作时间:工作天数为330天/年,工作时间为24小时/天,年小时数为7920小时。2、药水:假设药水成本为2.5元/平。3、设备:假设设备价格为800万元/台,宽幅为1.6米,线速为4米/分钟。
3) 情景三:实现规模化量产(产能利用率为70%),良率达到95%的情况。1、药水:假设药水成本为2元/平。2、设备:假设设备价格为600万元/台,宽幅为1.7米,线速为6米/分钟。
经测算,在情景一的情况下,一步法复合铜箔综合成本为6.78元/平,较传统铜箔成本高出40%左右,降本空间巨大。根据三孚新科调研纪要显示,一步法可以通过降低药水用量、提升设备生产速率、以及提升宽幅来实现降本。随着设备生产效率持续提升和工艺 技术不断迭代,在情景三的理想情况下,一步法复合铜箔综合成本可以降到2.67元/平, 相较于3.91元/平的传统铜箔,整体成本可下降32%左右,成本优势得以显现。
良率和设备线速对PET复合铜箔成本的影响较大。我们基于良率和设备线速对PET复合铜 箔进行敏感性分析,在设备线速为8米/分钟,良率为80%的情况下,PET复合铜箔单位成 本为2.79元/平。随着未来产品设备的优化和工艺成熟,若设备线速能够提升至12米/分 钟,良率提升至90%,则PET复合铜箔成本能够进一步降低至2.45元/平。
04
复合铜箔市场空间测算:新能源车+储能双轮驱动,替代空间广阔
我们根据以下假设对PET复合铜箔市场空间进行测算:
1)根据EVTank数据,2022年全球 新能源车销量为1082万辆,预计到2025年销量有望超过2507万辆,到2030年销量将超过 5542万辆;
2)根据市场需求测算,2023-2030年全球锂电池出货量分别为1206、1610、2087、2560、3108、3760、4531、5443GWh;
3)假设复合铜箔渗透率将逐年提升,则2023- 2030年渗透率分别为2%、5%、10%、15%、18%、20%、22%、25%;
4)根据产业调研,假设 1GWh电池所需阴极薄膜材料面积为1200万平米,同时假设2022年PET复合铜箔价格为6.5 元/平,未来价格每年下降5%。
5)根据东威科技披露,1GWh电池需要配备2台真空镀设备 和3台镀膜设备,随着设备生产效率和良率的提升,假设设备需求量逐年递减5%;同时假 设磁控溅射设备和水电镀设备2022年价格分别为1500万元/台、1200万元/台,价格每年 下降5%。
据测算,到2025年,PET复合铜箔渗透率将提升至10%,对应25亿平需求,市场空间有望 达到140亿元,设备空间将超过101亿元。远期来看,2030年PET复合铜箔渗透率有望提 升至25%,需求达到163亿平,市场空间有望达到704亿元,设备空间将达到395亿元。
复合铜箔渗透率提升,未来市场空间广阔。我们基于2025年复合铜箔渗透率和全球锂电池出货量对PET复合铜箔市场空间进行敏感性分析,假设2025年复合铜箔渗透率的区间跨度为5-25%,全球锂电池出货量区间跨度为1800-2200GWh。随着未来设备技术逐步成 熟,渗透率有望加速提升,若2025年复合铜箔渗透率提升至20%,全球锂电池出货量达到 2000GWh,则2025年PET复合铜箔市场空间有望达到268亿元。
05
复合铜箔:适用于对安全性敏感的高端电池产品
复合铝箔是一种由铝箔和聚合物薄膜复合而成的材料,通常用于电池正极集流体。在锂 电池中,由于正极电位高,铜箔在高电位下容易被氧化,而铝的氧化电位高,且铝箔表 层有致密的氧化膜,对内部的铝也有较好的保护作用,因此铝箔常用作正极集流体材料。复合铝箔对锂电池安全性的提升较大,产业化进程快于复合铜箔。
电池内短路是导致锂电池热失控的直接原因。根据ScienceDirect的数据,正极铝箔在短路下的热失控问题 较其他位置更为严重,因此使用单边复合铝箔对电池安全性提升较大。同时,复合铝箔 产业化进程快于复合铜箔,主要是因为铝和高分子膜的结合力比铜要强,无需进行磁控 溅射,制作工艺更为简单,目前复合铝箔主要采用真空蒸镀一步法进行生产。根据金美 新材公告,公司已于去年11月率先实现8微米复合铝箔的量产。
复合铝箔降本空间有限,目前定位为对安全性要求较高的高端产品。生产工艺来看,由 于铝的化学性质活跃,不适用于效率高的水电镀。复合铝箔目前仅由真空蒸镀法镀膜, 生产效率较低,加工成本大幅提升,目前价格远高于传统铝箔7-10倍左右。原材料成本来看,铝非贵金属,其价格本身较低。
相较于传统铝箔,复合铝箔的原材料成本仅降低 20%,而复合铜箔可降低64%,因此复合铝箔相较于铜箔所带来的降本幅度较小。能量密度来看,由于铝本身密度较低,仅为高分子膜密度的2倍,而铜密度为高分子膜密度的6 倍,所以置换为高分子膜后复合铝箔在提升能量密度幅度上小于复合铜箔。因此相比于 复合铜箔,复合铝箔适合应用于对成本不敏感,但对安全性要求较高的高端车和对减薄 要求较高的消费电池领域。
原文始发于微信公众号(锂电产业通):复合集流体,蓄势待发!
新能源汽车的快速发展带动了动力电池的高速增长。动力电池生产流程一般可以分为前段、中段和后段三个部分。其中,前段工序包括配料、搅拌、涂布、辊压、分切等,中段工序包括卷绕/叠片、封装、烘干、注液、封口、清洗等,后段主要为化成、分容、PACK等。材料方面主要有正负极材料,隔膜,电解液,集流体,电池包相关的结构胶,缓存,阻燃,隔热,外壳结构材料等材料。 为了更好促进行业人士交流,艾邦搭建有锂电池产业链上下游交流平台,覆盖全产业链,从主机厂,到电池包厂商,正负极材料,隔膜,铝塑膜等企业以及各个工艺过程中的设备厂商,欢迎申请加入。
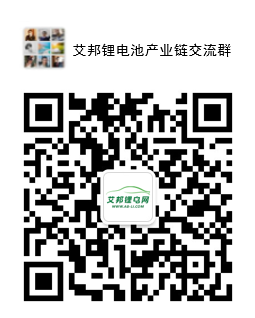
长按识别二维码关注公众号,点击下方菜单栏左侧“微信群”,申请加入群聊