近年来,锂电池行业的发展受到越来越多的关注。锂电池因其自身优势,在新能源汽车、储能、消费电子等领域得到广泛应用。但随着锂电池材料技术的进步和成本下降,其市场潜力正在逐渐被挖掘。
复合箔作为一种新型功能材料,被广泛应用于锂离子电池领域。随着国内复合箔生产企业的技术不断进步,以及下游应用领域需求的增加,复合箔逐渐受到关注,并在国内掀起了一波热潮。
广汽埃安发布弹匣电池 2.0,整包枪击后未发生起火和爆炸,内部复合集流体材料在电池短路时PET熔断,阻止电流流通和升温,极片断裂时PET不易刺穿隔膜,提供电池安全性。
复合集流体导电层较薄,局部短路易熔断,穿刺毛刺小,高分子材料层熔点低快速切断失效电路,有效提高电池安全性。
复合集流体代替传统集流体减重降本
传统铜箔在“铜价+加工费”模式定价下,原材料成本占比较大。复合铜箔相比于 6μm 传统铜箔原材料减重55%,复合铝箔相比于12μm传统铝箔减重64%。复合箔材缩减金属用量,减少箔材单位面积成本。
复合集流体提高能量密度
复合铜箔使用低密度的高分子材料置换部分金属铜,能够降低集流体重量和厚度,提升电池能量密度10%以上。
真空磁控溅射、真空蒸镀设备的良率和走速能否提升,直接关系到复合集流体项目的拉线效率和投资成本,进一步决定下游企业的导入力度。
近两年,随着产学研各界对复合集流体的关注度和研发投入大幅提升,真空镀膜设备工艺不断突破。
PVD镀膜设备助力复合集流体进一步发展
未来趋势——一步法:低投入,高产出
PVD一步法在3.0~4.5μmPET/PP直接镀铜1μm,无需使用化学电镀等湿法工艺,仅通过干法工艺便可一次完成双面铜膜。减少其他生产环节,提高良率,实现增效。
相比二步法和三步法,一步法的优势主要集中在:投资少,所有工序都在同一台设备上完成;镀膜减少基材卷绕传动的装夹次数,提高成品率;取消化学电镀工序,减少环境污染。
当前主流——两步法:复合铜箔RTR PVD溅射铜+化学电镀增厚1μm
面对复合铜箔磁控溅射工序里面存在的箔材穿孔、铜膜结合力差、产能瓶颈等三大难题,HCVAC进行了针对性的工艺迭代。
磁控溅射靶设计技术:溅射靶是高端镀膜设备的核心技术,涉及磁控靶设计技术,膜厚均匀性模拟分析技术,真空磁场分布模拟仿真技术,真空等离子体分布模拟仿真技术等。HCVAC设计的磁控溅射靶具有高膜材利用率、高膜层均匀性、高良率等特点,靶材利用率>85%。
电子束增强离子清洗装置技术:HCVAC通过创新性增强了等离子体能量、浓度、离化率和活性,使增强的等离子体具有强效的离子清洗刻蚀活化功能,也具有高效的加热和辅助沉积功能,可以彻底清洁基材,去除表面杂物,有效增强了膜/基结合力,避免铜层与基膜脱落现象的发生。
超低温镀膜技术:HCVAC自主研发超低温镀膜专利技术,使基材紧贴镀膜辊充分冷却,高沉积速率低温溅射工艺。
卷对卷真空镀膜设备设计技术:HCVAC采用模块化设计概念,带材卷绕系统、等离子体预处理、磁控溅射系统、在线测量和工艺控制系统等综合技术应用。使膜层均匀性好,沉积效率高,镀膜速度快。
HCVAC通过以上几大PVD工艺技术,改善箔材穿孔状况、提高铜膜结合力、提升产能,极大提升生产效率,进一步增强下游电池厂与车企导入设备的信心。
目前,HCVAC研发的复合铜箔 PVD 磁控溅射卷绕镀膜设备,实现在厚度3.0~4.5μm、幅宽600~1650mm PET/PP等塑料薄膜表面一次完成双面镀铜膜,设备工艺走速0.5-30m/min。从复合铜箔领域来看,目前HCVAC磁控溅射设备已实现量产,完全能满足市场需求。
PVD镀膜设备提高产能,降低成本,推进复合集流体降本增效
从上述表格可以看出,随着产能上升,PVD真空镀铜膜成本逐步下降,设备的不断更新进步,在提高产能的同时能有效降低设备成本及能耗指标,复合集流体PVD生产实现持续降本增效。
一步法:复合铝箔RTR PVD蒸发铝膜1μm
常规蒸发镀膜技术仍存在以下难题:
飞溅颗粒和针孔缺陷:飞溅颗粒吸附于基材表面经镀膜后,脱离基材而形成未镀区域(针孔缺陷),未脱离基材而形成凸起的结瘤(颗粒缺陷)。
热损伤:蒸发过程中产生的高温及蒸发材料对处于镀膜主辊冷却保护范围之外的柔性薄膜造成热损伤,起皱,断膜。
单炉和多炉对比:由于静电吸附力减小,镀铝后基材产生弹性变形,热损伤的累积,在相同条件下单炉也会出现一些热损伤。
HCVAC通过自主研发PVD RTR蒸发镀铝膜技术,超薄复合铝箔 PVD 蒸发卷绕镀膜设备,实现在厚度4.5~6.0μm、幅宽600~1700mm PET/PP塑料薄膜表面一次完成双面蒸镀铝膜,设备工艺走速10-100m/min,攻克大规模快速蒸发沉积厚铝膜难关。
复合铝箔的制备工艺相比传统铝箔压延工艺难度更大,以PVD蒸镀工艺为核心,通过高温熔化金属材料,在PET/PP塑料薄膜双面沉积铝膜,使其两面具有导电性。
复合铝箔蒸镀工艺相比于磁控溅射速度更快,效率更高,但由于高温易使基膜变形,在镀铜过程中较少使用;铝的熔点远低于铜,因此蒸镀的温度可以控制在相对更低的水平,可减少高温使基膜变形等问题的发生,因此蒸镀更适合复合铝箔的制备。
复合铝箔无需使用化学电镀等湿法工艺,仅通过干法工艺便可一次完成双面铝膜。复合铝箔基膜厚度比较厚,在4.5-6.0μm左右,制备过程中击穿断裂等风险下降,蒸镀工艺效率得到提升,因此无需采用化学电镀工艺做增厚处理,在一定程度上减轻了干湿法工艺转换过程对良率的影响。
广东汇成真空科技股份有限公司是一家研发、生产和销售PVD镀膜设备、光学镀膜设备、卷绕镀膜设备、连续式镀膜设备、半导体PVD/ALD设备等真空应用解决方案的国家高新技术企业,国家工信部授予“专精特新‘小巨人’”企业称号,成立广东省博士工作站。
4月27日,艾邦高分子将在苏州知音温德姆酒店举行第二届动力电池复合集流体大会,届时广东汇成真空高层代表将发表“PVD技术助力复合集流体降本增效”的主题演讲。敬请期待!
原文始发于微信公众号(锂电产业通):一步法PVD技术,助力复合集流体降本增效
新能源汽车的快速发展带动了动力电池的高速增长。动力电池生产流程一般可以分为前段、中段和后段三个部分。其中,前段工序包括配料、搅拌、涂布、辊压、分切等,中段工序包括卷绕/叠片、封装、烘干、注液、封口、清洗等,后段主要为化成、分容、PACK等。材料方面主要有正负极材料,隔膜,电解液,集流体,电池包相关的结构胶,缓存,阻燃,隔热,外壳结构材料等材料。 为了更好促进行业人士交流,艾邦搭建有锂电池产业链上下游交流平台,覆盖全产业链,从主机厂,到电池包厂商,正负极材料,隔膜,铝塑膜等企业以及各个工艺过程中的设备厂商,欢迎申请加入。
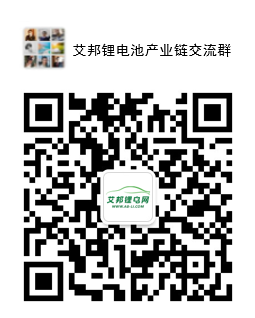
长按识别二维码关注公众号,点击下方菜单栏左侧“微信群”,申请加入群聊