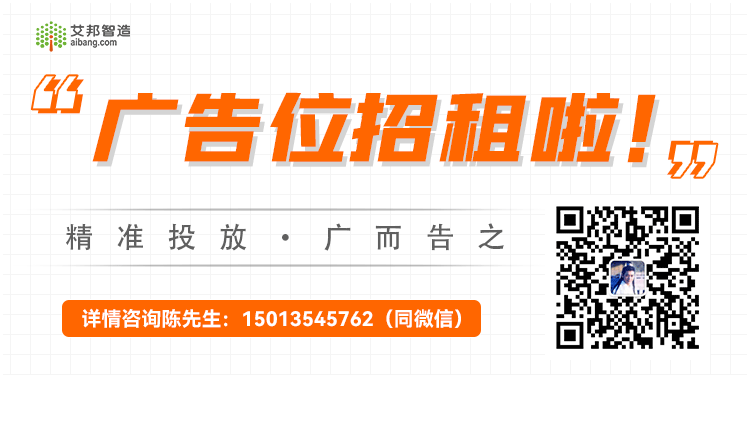
1. 前言
近二十年来,激光加工技术已成为发展最快的高新技术之一,为传统制造业改造提供了充足支持。相较于传统极耳焊接、极片切割模式而言,激光焊接、激光切割模式可以实现自动化操作,并解决毛刺、露白、掉粉等一系列问题,为锂电池性能的提升提供依据。因此,从激光加工技术的应用入手,探究极耳焊接与极片切割工艺具有非常突出的现实意义。
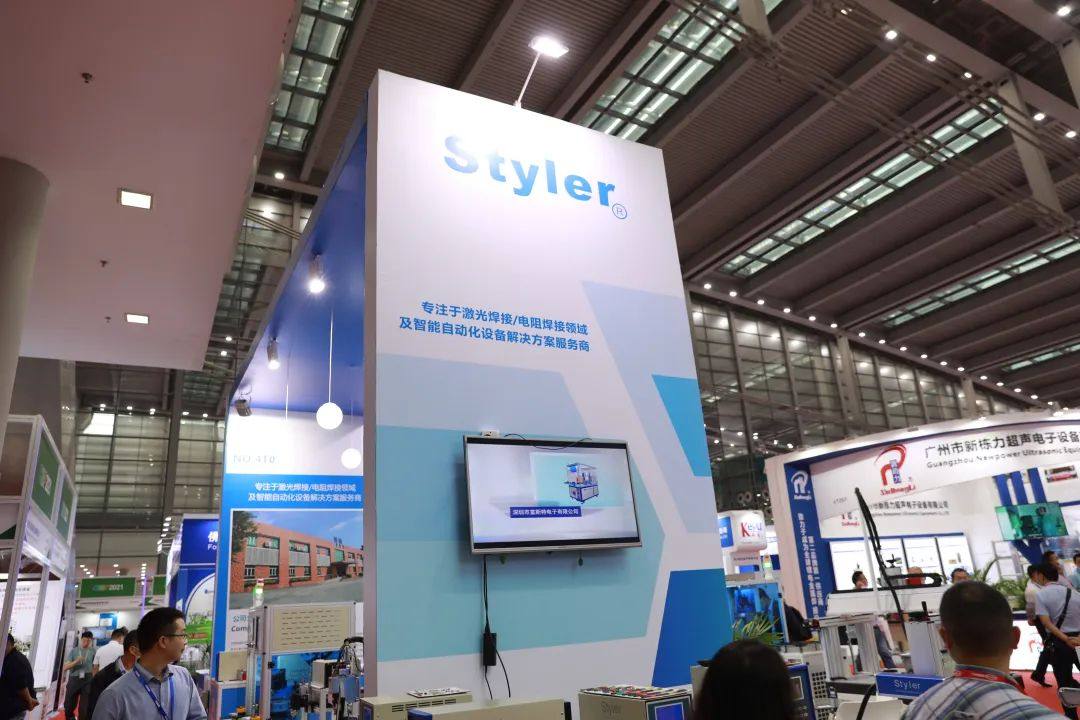
2. 激光焊接与激光切割的原理
2.1激光焊接
激光焊接主要是将高能量密度激光束作为热源,在功率密度小于104~105W/cm2时,经热传导加热工件表面,进行缓慢焊接,焊接熔深较浅;或者在功率密度超过105~107W/cm2时,通过控制激光脉冲峰值功率、宽度、重复频率、能量促使工件熔化并形成特定熔池,进行快速焊接,焊接熔深较大。
2.2激光切割
激光切割主要指利用激光切割材料,需要借助光学器件,引导输出高功率激光束。同时根据激光器内运动控制系统跟踪待切割工件轨迹,对准材料聚焦激光束,促使材料发生熔化、蒸发、燃烧、吹散等反应,获得表面光洁度较高的边缘。
3. 激光焊接在极耳焊接中的应用
3.1焊接装置选择
根据极耳焊接要求,焊接加工者可选择半自动焊接装置或全自动焊接装置。前者主要为手持式激光焊接机,其主要为圆盘结构,每间隔90°进行了V型槽开设,V型槽内可放置电池圆柱体零件,压紧零件后聚焦激光束至焊接部位,每焊接一个零件进行90°的转动,第二个焊接点则转动0.50mm;后者则是通过直筒漏斗方式上料,每经过一个“圆坑”、V型槽分别自动放入电池盖、待焊接电池主体,进行自动焊接。常用的激光焊接装备为SOUPACT紧凑型激光拼焊设备、泰德激光焊接系统等。
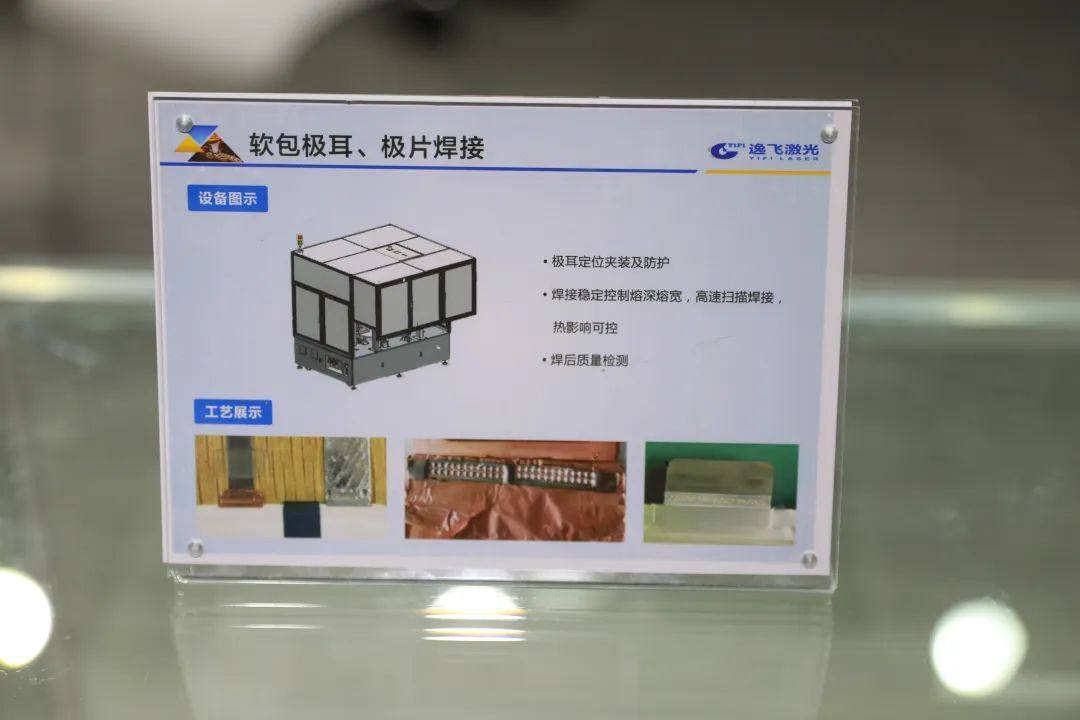
3.2焊接参数设置
考虑到当前软包锂离子电池为多种负极铝与铜汇流片焊接模式,铜极耳厚度在0.2–0.5mm左右,铝极耳焊接厚度在0.2~0.6mm左右。因此,在激光焊接极耳时,需要设定激光波长为1064nm,激光功率为110W~200W,光斑28μm,激光扫描速度与脉冲频率分别为500mm/s、200kHz,重复频率为0.4~20MHz,脉冲宽度为50–120ns。并控制极耳焊接缝隙宽度在1.2~2.4mm内,焊接缝隙深度在1.2~1.8mm内。同时保证极耳宽度精度与极耳间距精度、极耳高度精度均小于等于±0.15mm。
当前,在极耳激光焊接过程中,半自动焊接方法应用较少,以全自动焊接较为常见。
在全自动焊接过程中,焊接流程如下:如图1所示,首先需要启动装置,开展待焊接零部件位置的检测,只有电池盖、待焊接电池主体均处于正确位置,方可启动焊接、转平、下料、移位等工序。
其次,在确定焊接零部件位置正确后,需要完成极耳的自动转平操作。因电池主体为自动放入,无法保证极耳处于水平位置,此时,就需要利用光电检测方式,待极耳转入水平位置后自动停止,保证后续压紧、焊接操作正常开展。同时因极耳对焊接平直度具有较高的要求,需要利用电磁去除装置将存在弯曲、扭动等与标准不相符的电池零件自动去除,防控“焊废”现象。
再次,在压紧过程中,主要依靠自动压紧装置,多为微机控制的四连杆式电磁自动机构,可在焊接前压紧极耳、安全阀,为激光穿透式焊接提供良好的条件。因每一锂电池焊接点位为2个(距离在0.50mm左右),因此,为保证电极接触的可靠性、安全性,需要重复启动2次压紧机构并进行激光器的2次焊接。
最后,焊接完毕后,将电池转入下道工序,实现自动下料。一般自动下料机构为永磁滚筒刮板滑道式,可以在角度、位置恰当的情况下,由磁铁吸附电池滚筒促使电池体由刮板进入弯曲下降的滑梯式滑道,经滑道进入下一道工序。
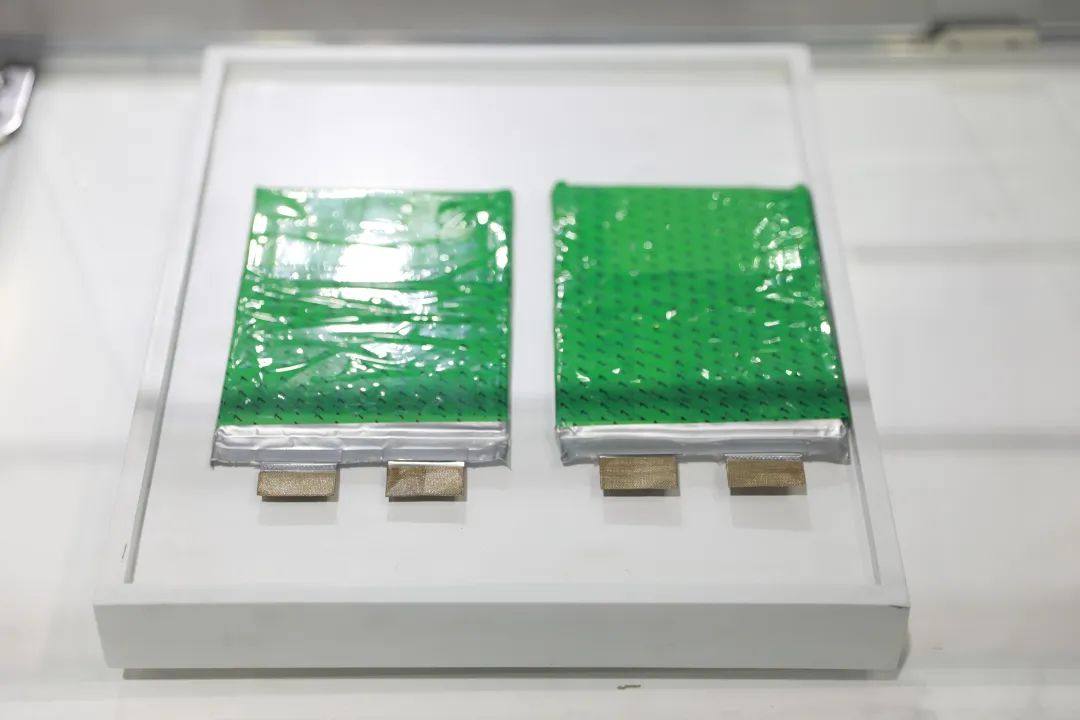
根据锂电池极片材质,可以选择不同的锂电池极片切割系统。比如,对于锂电池负极铜箔,可以选择1064nmMOPA型光纤激光器,其峰值功率密度为2.4×106W/mm2,可以通过对种子源的电进行调制,在兆赫兹工作频率内实现几纳米到几十纳米的“窄脉宽”切割。再如,对于锂电池正极铝箔,可以选择脉冲达到皮秒级的皮秒激光器,其可以通过进行种子源锁模,获得超窄脉冲信号。进而经放大级别输出,在几十兆赫兹工作频率内实现几纳米的“超窄脉宽”切割。同时皮秒激光器可以利用三倍频技术,将1064nm近红外激光向355nm紫外光、532nm绿光转化,满足多种类别材料加工需求,并在激光脉宽小于材料电-声弛豫时间时实现“冷加工”。
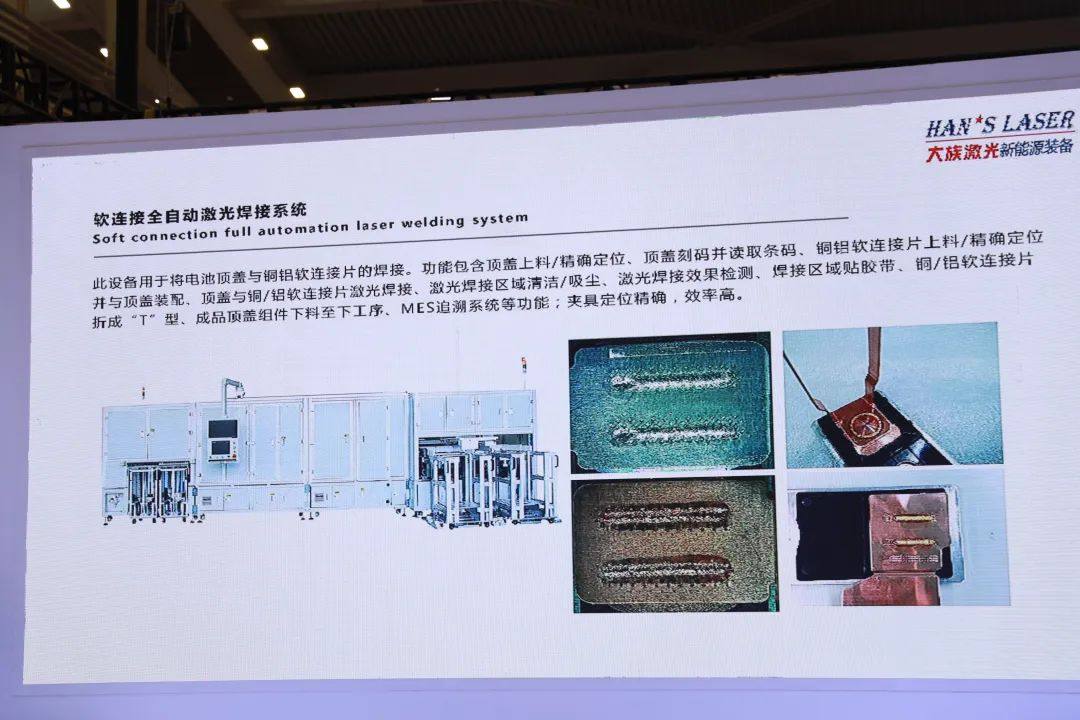
在应用1064nmMOPA型光纤激光器切割8.0μm铜箔(锂电池负极)时,可以设定脉宽为20ns,工作频率与单脉冲能量分别为760kHz、0.13mJ,改善铜箔切割毛刺问题,并将毛刺尺寸控制在10μm内,同时减少锂电池铜箔极片切割飞溅、熔融层尺寸误差。部分情况下,为了减少熔融层“鱼鳞纹”现象,也可以将脉冲频率进行进一步提高,杜绝熔融重新凝结层。需要注意的是,在将脉宽一定、调高平均功率的同时,还需要根据激光器聚焦需要,调整焦点光斑直径为60μm,调整铜箔切割时振镜走笔速度为800mm/s。考虑到铜箔具有高热导率,材料吸收的激光能量不仅可以发生熔融汽化切口,而且可以沿着切口向材料内部、周边传递,形成熔融区、热扩散区多个区域。一般熔融区下方会出现显著的亮白色+红色+黄色热影响带,由近切口段向远处分布。
在应用9.1W皮秒激光器532nm绿光激光器切割铝箔正负极片时,可以设定脉宽为10ps,切割速度为1000mm/s,重复频率为300kHz,缩小正极片熔融重新凝结区域,减弱熔融区下方亮白色+红色+黄色热影响带,消除白色光亮层、红色热扩散层。而对于铜箔正负极片,因其电声弛豫时间为57.5ps>10ps(激光脉宽),极易致使电子获得能量无法满足与晶格完全交换热量需求,因此,可以依托高能激光环境,围绕最外层电子大量能量电离与内层电子碰撞电离过程,以高价正电母离子带离为对象,观察切口热效应。根据观察结果,进行切割参数的调整,或者进行辅助气体的应用,如将常温辅助气体变更为低温辅助气体等。
在锂离子电池极片激光切割过程中,常用的切割方法为立式、卧式,前者用于叠片式电池切割,需要在传输带上水平运输极片,在极片到达激光发射装置下进行切割;后者多用于卷绕式电池极片切割,并通过在极片上方设置吸尘罩及时吸附切割过程中产生的粉尘。考虑到在极片上方吸尘的方式极易导致极片切割不平整、切割精度下降问题出现,可以通过激光发射装置、水平传输驱动装置、锂离子电池极片切割吸附装置、切割模块循环输送装置运行过程的严格控制,去除极片上方吸尘罩,保证极片切割精度。即将锂离子电池极片切割吸附装置设置在驱动模块传输的锂离子电池极片上方,促使其在循环输送模块第一输送带边缘与锂离子电池极片同时移动。在切割模块移动到切割位置后,由控制器直接启动激光发射装置,对锂离子电池极片进行切割。对于电池极片切割过程中出现的废渣则通过切割模块上设置的切割轨迹槽排出,同时通过切割模块中设置的负压通道吸附细小尘土。
综上所述,利用激光加工技术,可以在保证极耳焊接、激光切割质量的同时,提高加工效率,并降低维护作业量,助力锂电池极片切割、极耳焊接加工效益的提升。因此,在极耳焊接、极片切割过程中,加工者可以根据加工需求选择恰当的激光器,如皮秒激光器、MOPA激光器、紫外激光器等,并进行激光器波长、脉宽、最大单脉冲能量等参数的调整,保证激光加工优势的充分发挥。
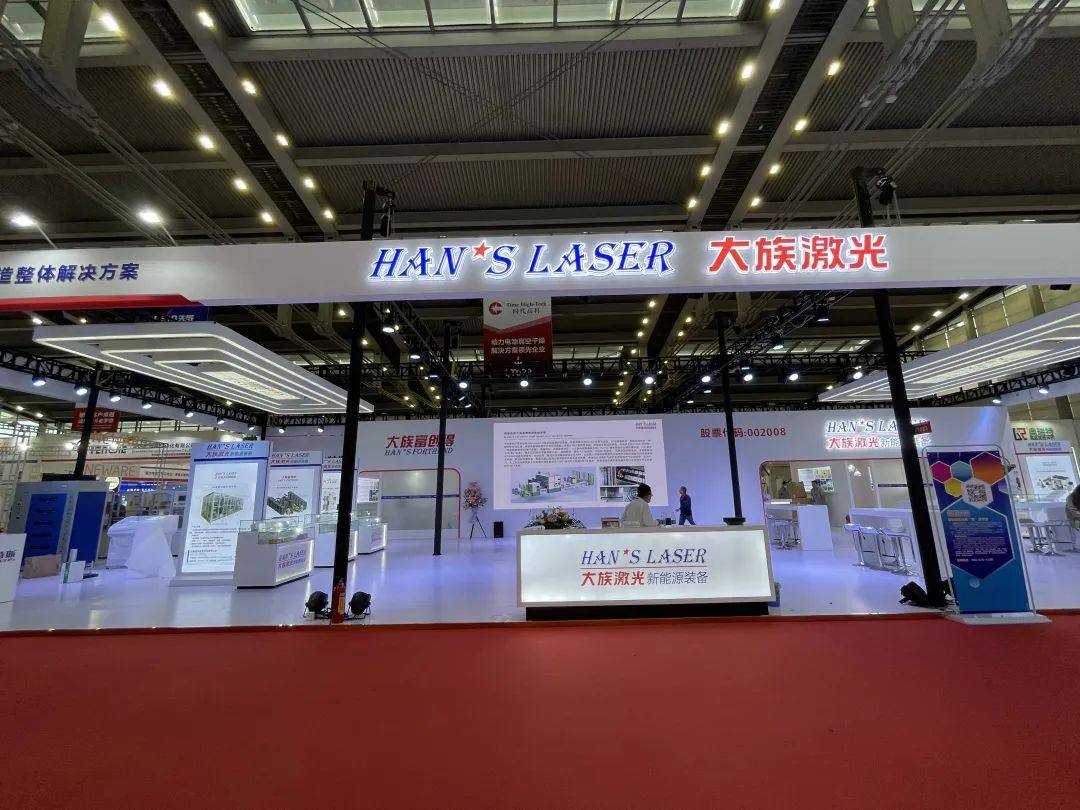
新能源汽车的快速发展带动了动力电池的高速增长。动力电池生产流程一般可以分为前段、中段和后段三个部分。其中,前段工序包括配料、搅拌、涂布、辊压、分切等,中段工序包括卷绕/叠片、封装、烘干、注液、封口、清洗等,后段主要为化成、分容、PACK等。材料方面主要有正负极材料,隔膜,电解液,集流体,电池包相关的结构胶,缓存,阻燃,隔热,外壳结构材料等材料。
为了更好促进行业人士交流,艾邦搭建有锂电池产业链上下游交流平台,覆盖全产业链,从主机厂,到电池包厂商,正负极材料,隔膜,铝塑膜等企业以及各个工艺过程中的设备厂商,欢迎申请加入。
长按识别二维码关注公众号,点击下方菜单栏左侧“微信群”,申请加入群聊