动力电池大规模制造启动,安全问题已经成为悬在行业头顶的达摩克利之剑,亟待解决。
电池的安全一般可以归纳为以下三个层面,电芯的固有安全、不同层级的防护安全以及法规/标准规范的(相对)可接受安全。目前,电芯的固有安全依旧是电池安全优先要解决的问题。
衡量电芯固有安全的一个重要方法就是强制其内部短路,测试其是否着火或爆炸以及电芯的压降和温升。
电芯强制内部短路测试的意义
引起电芯内部短路的因素非常多,包括隔膜的特性、开发和设计、制造流程、包装和运输、组装和应用、使用、维护和再利用等等,这些场景都有可能引起电芯的间接或直接内部短路。电芯强制内部短路测试,就是通过模拟极端情况来验证电芯是否发生内部短路以及发生内部短路时是否会着火或爆炸,进而识别电芯的固有安全特性以及电池系统的安全特性。
多数电池标准规范了电芯强制内部短路测试,同时,众多电池及电池应用产品的品牌商将该测试项目作为企业规范。电芯强制内部短路测试广泛应用在对电芯的材料、开发、设计、制程乃至电池模组、电池系统的合规评价上。
- IEC 62133-2:2017/AMD1:2021(便携式电池)
- Appendix 9 (edition 1)(便携式电池)
- JIS C 62133-2:2020(便携式电池)
- IEC 62660-3:2016(动力电池)
- IEC 62619:2017(工业、储能电池)
1. 电芯的预处理
1)电芯需要在20 °C±5 °C的环境下按照厂家推荐的方法充电,然后以0,2 It A放电至厂家规定的放电截止电压;
2)电芯按照厂家定义的充电上限温度和下限温度放置1-4小时;
3)以最大充电电流和上限充电电压为电芯充电,直到电流减少到0,05 It A。
2. 电芯的拆解
电芯的拆解是电芯强制内部短路测试中的关键一步,但也极具挑战性和争议性。
3. 卷芯的挤压
1)卷芯表面温度稳定在充电上限温度和下限温度的2度范围内后,准备挤压;
2)压具以0,1 mm/s的速度压向卷芯,同时以每秒100次以上的速度监测卷芯电压;
3)当检测到内部短路引起电压下降时,应立即停止挤压,并将压具保持在该位置30秒后释放压力。如果与初始电压相比,电压下降超过50 mV,则确定发生了内部短路。在压降达到50 mV之前,如果压力达到800 N(圆柱型电池)或400 N(方型电池),则立即停止挤压。
4. 合规的判定
测试过程中不起火(企业可能有更加严格的允收标准)。
DEKRA德凯广州电池资深项目工程师表示:当前版本的IEC 62133-2电芯强制内部短路测试仅针对非固态电解液,且只针对瑞士、法国、韩国和日本四个国家,即我们通常说的国家差异。考虑电池的应用普适性和安全性,我们建议您全面采用该测试。
来源:电芯为什么要进行强制内部短路测试?
原文始发于微信公众号(锂电产业通):电芯为什么要进行强制内部短路测试?
新能源汽车的快速发展带动了动力电池的高速增长。动力电池生产流程一般可以分为前段、中段和后段三个部分。其中,前段工序包括配料、搅拌、涂布、辊压、分切等,中段工序包括卷绕/叠片、封装、烘干、注液、封口、清洗等,后段主要为化成、分容、PACK等。材料方面主要有正负极材料,隔膜,电解液,集流体,电池包相关的结构胶,缓存,阻燃,隔热,外壳结构材料等材料。 为了更好促进行业人士交流,艾邦搭建有锂电池产业链上下游交流平台,覆盖全产业链,从主机厂,到电池包厂商,正负极材料,隔膜,铝塑膜等企业以及各个工艺过程中的设备厂商,欢迎申请加入。
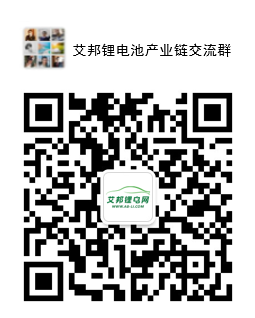
长按识别二维码关注公众号,点击下方菜单栏左侧“微信群”,申请加入群聊